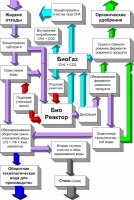
Ультразвуковые технологии для сельского хозяйства
Как фермеру открыть свое газовое и нефтяное месторождение,
или производство Биогаза и Биодизеля
О двух животрепещущих темах в Украине – сельское хозяйство и цены на газ – не говорят и не пишут только ленивые. Эти темы не сходят со страниц газет, экранов телевидения и являются «болью в сердце» всех политиков. Все что-то говорят, но никто ничего не предлагает и, тем более, не делает.
В этой статье мы объединим некоторые проблемные вопросы сельского хозяйства и высоких цен на газ, рассмотрим реальную возможность комплексной переработки отходов животноводства, получения из них высококачественных удобрений, биогаза и биодизеля, а также снятия экологической нагрузки на природную окружающую среду от деятельности крупных животноводческих ферм и коммунальных полигонов захоронения отходов.
1 Все новое – это давно забытое старое
Вернемся немного в прошлое. В СССР в 80-е годы разрабатывалась научно-техническая программа «Трансформации продуктов фотосинтеза» (сокращенно – ТПФ). Генеральная линия программы ТПФ – внедрение в агропромышленный комплекс не просто отдельных биотехнологических процессов, а целых биотехнологических систем, позволяющих в максимальной степени использовать растительное сырье, резко снизить затраты электроэнергии, сделать сельскохозяйственное производство экологически чистым и безотходным… Одна из концепций – интегрированная система переработки отходов и энергосбережение жилого комплекса, а проще говоря, создание экологически замкнутого хозяйства, которое не будет загрязнять окружающую природную среду никакими отходами, и к которому не нужно будет подводить ни электричество, ни газ: всю необходимую ему энергию дадут солнечный коллектор, тепловые насосы, и, конечно же, биореактор, где будут перерабатываться канализационные стоки и отходы.
Красивая мечта, воплощение которой в жизнь так и не произошло. Но одним из центральных элементов этой системы был «биореактор для семейной фермы». Построить его для себя сегодня может каждый желающий фермер. Рассказывая о том, как построить установку для производства биогаза, мы будем показывать пути интенсификации процессов и технологии с помощью ультразвука. Применение мощного ультразвука для небольших фермерских хозяйств – дорогое удовольствие. Но специалисты больших предприятий смогут увидеть и понять технологический процесс и те выгоды, которые им принесет внедрение ультразвуковых технологий на своих производствах.
2 Навоз – ненужные отходы или полезное сырье?
Далее рассмотрим не совсем аппетитную сторону любой животноводческой фермы – навоз. По приблизительной оценке, каждая овца за год «вырабатывает» около 0,8 тонн навоза, свинья – 1,5 т, лошадь – 6-7 т, корова – 8-10 т, курица – 5-6 кг помета в год. Но, в зависимости от состава кормов и подстилки, выход навоза, скажем на одну буренку, может повышаться до 12-14 т. Стандартный свинокомплекс на 108 тысяч голов дает столько же отходов, сколько и город с населением в миллион человек. Для свинокомплексов в 20 тысяч голов проектируются навозохранилища объемом 80 тысяч кубометров и более, которые, даже при трехэтажной высоте конструкции, занимают целый гектар земли и стоимость их немалая.
Теперь еще некоторые цифры: переработка бесподстилочного навоза от 10 голов крупного рогатого скота позволяет получить в сутки около 20 м3 биогаза, от 10 свиней – 1-3 м3, от 10 овец – 1-1,2 м3, от 10 кроликов – 0,4-0,6 м3. Тонна соломы дает 300 м3 биогаза, тонна коммунальных отходов – 130 м3. Для сравнения, потребность в газе односемейного дома, включая отопление и горячее водоснабжение, составляет, в среднем, 10 м3 в сутки, хотя может и сильно колебаться в зависимости от теплоизоляции дома.
Навоз всегда считался ценным удобрением. Но это, так сказать, классический навоз, по преимуществу конский или коровий, да еще щедро сдобренный соломой из подстилки. На современной птицефабрике, ферме или свинокомплексе навоз совсем другой. Подстилки там и в помине нет – навоз смывают водой (научились у Геракла), объем стоков от этого увеличивается во много раз, а концентрация сухих веществ, в которых заключена «удобрительная» ценность навоза, уменьшается до нескольких процентов.
Все это гигантское количество жижи приходится где-то хранить – хотя бы в период, когда удобрения не вносят. Выдерживать навоз нужно еще и для того, чтобы обезвредить всегда присутствующие в нем патогенные микробы, яйца гельминтов и семена сорняков, которые, после внесения в почву, немедленно пойдут в рост.
Кроме того, при хранении трудно предотвратить просачивание такого жидкого навоза в землю, в подземные воды, в реки и водохранилища. Да и окружающую атмосферу он заражает зловонием. Обезвреживание навозных стоков, особенно со свинокомплексов и птицефабрик, - серьезная экологическая задача в масштабах всей страны.
3 Такие разные микробы
Один способ обезвреживания навоза, а также любых других органических остатков, известен давно – это компостирование. Отходы складывают в кучи, где они под действием микроорганизмов – аэробов понемногу разлагаются. При этом содержимое кучи разогревается примерно до 60 °С и происходит естественная пастеризация – погибает большинство патогенных микроорганизмов и яиц гельминтов, а семена сорняков теряют всхожесть. Но качество удобрения при этом страдает: пропадает около 40 % содержащегося в нем азота и значительное количество фосфора. Пропадает и энергия, потому что впустую рассеивается тепло, выделяющееся из недр кучи, - а в навозе заключена почти половина всей энергии, содержащаяся до этого в кормах. Отходы деятельности свинокомплексов для компостирования просто не годятся, они слишком жидкие.
Но есть микроорганизмы – анаэробы, дающие возможность другого пути переработки органического вещества – сбраживания без доступа воздуха, или анаэробная ферментация. Аналог биореактора – брюхо любой буренки, пасущейся на лугу. Там, в коровьем желудке, обитает целое сообщество микроорганизмов. Одни из них – это метанобразующие бактерии. Благодаря им одна корова производит в сутки до 500 литров метана. У метанобразующих бактерий необычный состав клеточных стенок, совершенно своеобразный обмен веществ, свои, уникальные ферменты и коферменты, не встречающиеся у других живых существ. Их даже считают продуктом особой ветви эволюции.
Примерно такое сообщество микроорганизмов и приспособили ученые-микробиологи для решения задачи – переработки отходов животноводческих ферм. По сравнению с аэробным разложением при компостировании, анаэробы работают медленнее, но зато гораздо экономнее, без лишних энергетических потерь. Конечный продукт их деятельности – биогаз, в котором содержится 60-70 % метана. Во всех прочих отношениях анаэробная ферментация ничуть не хуже компостирования. А самое важное то, что таким способом прекрасно перерабатывается жидкий навоз со свинокомплексов: пройдя через биореактор, эта зловонная жижа превращается в прекрасное удобрение. На одной из свиноферм на 2500 свиней в Латвии два реактора, по 75 м3 каждый, перерабатывали все отходы с фермы в высококачественное удобрение и давали хозяйству 300-500 м3 газа в сутки. При сегодняшних ценах на газ строительство биореактора становится экономически выгодным.
Но здесь есть еще одна тонкость. Бактерии метанового брожения, в отличие от аэробов при компостировании, сами тепла не выделяют, а рабочая среда для них должна быть теплая. Для одних, термофильных, нужно поддерживать температуру около 55 °С, для других, мезофильных, около 37 °С. Вопрос о том, какой вариант лучше, учеными еще не решен. Но, так или иначе, в нашем климате большую часть года реактор необходимо подогревать. На это уходит примерно треть полученного газа. Но даже в таких условиях остающегося биогаза хватит на нужды фермы (отопление, горячая вода и пр.).
Естественно, что на больших животноводческих комплексах экономические показатели и окупаемость оборудования будут значительно выше, чем в небольших фермерских хозяйствах. Конечно, экономика получилась бы совершенно иная, если бы к энергетическому эффекту прибавить еще эффект экологический, переведя его в денежное выражение и экономические выгоды. Но как это сделать, пока еще, кажется, не знает никто.
4 Как построить биореактор
Биогазовая установка может быть создана в любом хозяйстве из простых, доступных материалов силами специалистов самого хозяйства. Ферментация навоза происходит в анаэробных (безкислородных) условиях при температуре 30-55 °С (оптимальная 40 °С). Длительность процесса ферментации, обеспечивающая обеззараживание навоза, не менее 12 суток. При применении ультразвука она может быть сокращена вдвое, т.е. до 6 суток.
Для анаэробной ферментации можно использовать как обычный, так и жидкий, бесподстилочный навоз, который легко подается в биореактор фекальным насосом.
При ферментации в навозе полностью сохраняются азот и фосфор. Масса навоза практически не изменяется, если не считать испаряемой воды, которая переходит в биогаз. Органическое вещество навоза разлагается на 30-40 %; деструкции подвергаются, в основном, легко разлагаемые соединения – жир, протеин, углеводы, а основные гумусосодержащие компоненты – целлюлоза и лигнин – сохраняются полностью.
При применении в этом процессе ультразвука степень разложения органики получается значительно выше. Благодаря выделению метана и углекислого газа оптимизируется соотношение C/N. Доля аммиачного азота увеличивается. Реакция получаемого органического удобрения – щелочная (pH 7,2-7,8), что делает такое удобрение особенно ценным для кислых почв. По сравнению с удобрением, получаемым из навоза обычным способом, данное повышает урожайность на 10-15 %.
Получаемый биогаз плотностью 1,2 кг/м3 (0,93 плотности воздуха) имеет следующий состав: метан – 65 %; углекислый газ – 34 %; сопутствующие газы – до 1 % (в том числе сероводород – до 0,1 %). Содержание метана может меняться в зависимости от состава субстрата (ферментируемого вещества в биореакторе) и технологии в пределах 55-75 %.
Содержание воды в биогазе при 40 °С – 50 г/м3; при охлаждении биогаза она конденсируется, поэтому необходимо принять меры к удалению конденсата (осушка газа, прокладка труб газопровода с нужным уклоном, вентили для продувки и пр.). В качестве осушителя можно использовать абсорберы, десорберы, висциновые фильтры (с кольцами Рашига).
Для газопроводов и обвязки используют стандартное газовое оборудование. Энергоемкость получаемого газа – 23 мДж/м3 или 5500 ккал/м3.
Основное
оборудование биогазовой установки –
герметичная емкость с теплообменником
(теплоноситель – вода, нагретая до 50-60
°С), устройства для ввода навоза и вывода
переработанного субстрата и для отвода
газа.
Так как на каждой ферме свои особенности удаления навоза, использования подстилочного материала, теплоснабжения, создать конструкцию типового биореактора невозможно. Его конструкция во многом определяется конкретными условиями, наличием материалов и средств.
Для небольшой биогазовой установки наиболее простое решение – использовать высвободившиеся топливные цистерны. Схема биореактора на базе стандартной топливной цистерны объемом 50 м3. Внутренние перегородки могут быть выполнены из металла или из кирпича; их основная функция – направлять поток навоза и удлинять его путь внутри реактора, образуя систему сообщающихся сосудов. На схеме перегородки показаны условно; их число и размещение зависит от свойств навоза – степени текучести, количества подстилки.
Биореактор из железобетона требует меньше металла, но более трудоемок в изготовлении.
Чтобы определить требуемый объем биореактора, нужно исходить из количества получаемого навоза, которое зависит как от численности и массы животных, так и от способа его удаления: при смывке бесподстилочного навоза общее количество стоков увеличивается во много раз, что нежелательно, т.к. требует увеличения затрат на подогрев биореактора. Если суточное количество стоков известно, необходимый объем биореактора можно определить, умножив это количество на 12 (поскольку минимальный срок выдержки навоза 12 суток) и увеличив полученное значение на 10 % (т.к. биореактор следует заполнить субстратом на 90 %).
Ориентировочная суточная производительность биореактора при загрузке навоза с содержанием сухого вещества 4-8 % – два объема газа на объем биореактора, т.е. биореактор объемом 50 м3 будет производить за сутки 100 м3 биогаза.
Подогревать субстрат в биореакторе до 40 °С можно различными способами. Удобнее всего использовать для этого типовые газовые водонагревательные аппараты типа АГВ-80 или АВГ-120, их ассортимент сегодня огромен.
Для поддержания оптимальной температуры теплоносителя необходимо снабдить биореактор системой автоматики. При питании водонагревательного аппарата получаемым биогазом (вместо природного газа) следует его отрегулировать, уменьшив подачу воздуха.
Можно также использовать для подогрева субстрата «ночную» электроэнергию. Аккумулятором тепла в этом случае служит сам биореактор.
Для уменьшения потерь тепла биореактор необходимо тщательно теплоизолировать. Можно устроить вокруг него легкий каркас, заполненный стекловатой; нанести на наружную поверхность слой пенополиуретана и пр.
Давление газа, получаемого в биореакторе (100-300 мм вод. ст.), достаточное для его подачи на расстояние до нескольких сотен метров без газодувок или компрессоров.
При запуске биореактора необходимо заполнить его субстратом на 90 % объема и выдержать не менее 12 суток, после чего можно подавать в него новые порции субстрата, извлекая соответствующее количество ферментированного продукта.
Примерные статьи затрат материалов и средств:
Техническая документация, согласования.
Оборудование и материалы:
цистерна;
насосы, фекальный или «навозный» (для подачи 3-5 м3 в сутки при использовании топливной цистерны объемом 50 м3);
трубопроводы диам. 80-100 мм;
изоляционный материал;
водонагревательные аппараты типа АГВ-80 или АВГ-120 – 2 шт;
арматура газовая и канализационная.
Строительные и монтажные работы.
Непредвиденные расходы (20 %).
Эксплуатационные расходы.
Биореактор объемом 50 м3 вырабатывает в сутки 100 м3 биогаза, из которых на долю «товарного» газа приходится, в среднем, около 70 м3 (остальное идет на подогрев биореактора), что составляет 25 тыс. м3 в год – количество, эквивалентное 16,75 т жидкого топлива. При «ожидаемой» цене на природный газ около 300 $ за 1 тыс. м3 биореактор может сэкономить около 7500 $ в год. Кроме того, при таком расчете не учитывается предотвращение загрязнения окружающей природной среды, стоимость получаемого высококачественного удобрения, а также увеличение урожайности в результате его применения.
Техническую документацию на строительство биореактора специалисты хозяйства (инженер-механик, строитель, энергетик, электрик) могут подготовить за несколько дней. В документацию должны входить: технологическая схема, план размещения биореактора и теплогенератора, потоки энергии и продуктов, трубопроводы, схема подключения насоса и осветительной арматуры, калькуляция (смета расходов). На генплане хозяйства нужно показать основные трубопроводы, подъездные пути, контур заземления и молниеотводы. Документацию необходимо согласовать с газовой инспекцией и службой пожарной охраны – это, наверное, самая значительная часть «финансовых» затрат.
При эксплуатации биореактора необходимо соблюдать все действующие нормы и правила работы с установками для сжигания природного газа. Биогаз имеет более узкий предел взрываемости, чем природный газ – от 6 до 12 % (вместо 5-15 % для природного). В документации следует предусмотреть наличие вентиляции, которая, согласно государственным стандартам, должна обеспечивать в помещении объемом до 300 м3 восьмикратный обмен воздуха в час.
Тепло, получаемое при сжигании биогаза, может быть использовано, кроме подогрева воды (отопление, горячее водоснабжение) и приготовления пищи и кормов, для отопления теплиц, а в летний период, когда биогаз в избытке, для сушки сена и других кормов или, при питании биогазом абсорбционного холодильника, для охлаждения продукции, например, молока. Можно также использовать биогаз для выработки электроэнергии, но это менее выгодно.
Если несколько небольших ферм или индивидуальных хозяйств расположены поблизости друг от друга, целесообразно организовать централизованную переработку отходов и получаемый биогаз подавать на фермы или в хозяйства по трубопроводам.
Есть еще одно направление использования биогаза – утилизация углекислотного газа, содержащегося в нем в количестве около 34 %. Извлекаемый углекислотный газ, путем отмывки (в отличие от метана он хорошо растворяется в воде), можно подавать в теплицы, где он служит «воздушным удобрением», увеличивая продуктивность растений.
5 Что может ультразвук?
Ультразвуковое поле, или по другому «макрозвук», в диапазоне частот 20-40 кГц и интенсивностью 0,5 Вт/см2 и более классифицируется как «мощный ультразвук». Воздействуя на твердые, газообразные и жидкие среды мощный ультразвук способен вызывать необратимые реакции в тепломассообменных процессах. Учитывая то, что интенсивность (плотность) ультразвука может быть 100 Вт/см2 и более, мы получаем уникальный «инструмент», привносящий в «озвучиваемую» (обрабатываемую ультразвуком) среду огромное количество энергии. В результате воздействия мощного ультразвука возникает целый ряд эффектов, явлений и сил, которые трудно или вообще невозможно получить никакими другими методами воздействия (электромагнитные, оптические, тепловые, химические и пр.).
Мощный ультразвук «заставляет» озвучиваемую среду колебаться с частотой 20 000-40 000 раз в секунду. В результате чего в десятки раз ускоряются химические реакции; в разы увеличивается теплопередача в теплообменных аппаратах; ультразвук способен «разрывать» молекулу воды на радикалы Н и ОН. При определенных амплитудно-частотных характеристиках и малой интенсивности ультразвукового поля можно создать условия для значительного ускорения роста и развития микроорганизмов.
В то же время при большой плотности ультразвуковой волны в жидкой среде в ультразвуковом поле уничтожается патогенная микрофлора (яйца гельминтов, кишечная, туберкулезная палочка, стафилококковые и пр.) без применения химических веществ (хлор, озон, перманганат калия и пр.).
Ультразвуковое воздействие на жидкость приводит к ее активной дегазации, удалению растворенных газов из жидкости.
Ультразвуковая кавитация и капиллярный эффект, возникающие в жидкости под действием мощного ультразвука, способствуют очистке фильтров и сеток, создают благоприятные режимы фильтрования суспензий с мелкодисперсными частицами.
Ультразвук способен создать псевдоожиженный слой твердых веществ, что, в свою очередь, способствует ускорению процессов сушки и является энергосберегающей технологией.
Украинскими учеными Института биоорганической и нефтехимии (ИБОНХ) АН Украины разработана технология концентрации субстрата, осветления технологической воды, переработки отходов свинокомплексов, как, впрочем, и любых других органических отходов, в высококачественное удобрение. Разработаны установки безреагентного обеззараживания стоков, работа которых основана на совместном воздействии мощного ультразвука, ультрафиолета (в диапазоне 185 и 254,7 нм) и электромагнитного поля. Разработаны методы интенсификации работы биореактора, концентрации и осушки метана до норм государственных стандартов для подачи его в газопровод.
Специалистами Научно-Производственной Лаборатории «Ультра Звуковые Технологии» разработано ультразвуковое оборудование промышленного назначения на современной элементной базе для работы в жестких эксплуатационных условиях, способное обеспечить высокий к.п.д. и необходимую энергию активации для различных технологических процессов. Вопрос лишь в востребованности этих технологий и оборудования.
Типовая технологическая схема комплексной переработки отходов животноводческих комплексов, очистных сооружений и прочих отходов органического происхождения на схеме.