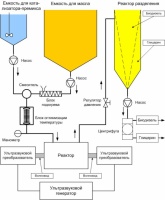
Биодизель – это просто!
Путешествуя летом по югу Украины, мы с Вами можем увидеть бескрайние поля подсолнуха, сои, рапса и прочих масляничных культур. Имея такое богатство в своих руках, сельхозпроизводители регулярно жалуются на нехватку дизтоплива, а также на «безбожные» цены на него. Резонный вопрос – почему? Наверное, они просто не знают того, что дизтопливо «растет» на их полях, или не понимают, что наладить его производство можно также в своем хозяйстве. Это значительно дешевле, чем купить новый зерноуборочный комбайн типа «Джон Дир» или «Клаас», а окупаемость необходимого оборудования намного выше. И, наверное, гораздо выгоднее продавать готовое биодизельное топливо, а не семена рапса (за бесценок) в Европу? Ответы на эти вопросы ищите сами, а мы расскажем Вам о технологии производства биодизеля и об оборудовании, которое для этого необходимо, дабы развеять миф «о невозможности решить проблемы с дизтопливом накануне посевной и уборочной страды».
Классический, традиционный способ и оборудование для получения биодизеля мы рассматривать не будем: этот, так называемый, «пакетный», или цикличный, способ с использованием тепла и механического смешивания весьма неэкономичен и давно устарел. Эффективной альтернативой этого способа является ультразвуковая технология, основанная на эффекте кавитации. Ультразвуковая кавитация обеспечивает необходимую энергию активации процессов для промышленного производства биодизеля.
Производство биодизельного топлива из растительных масел (сои, рапса, подсолнечника и т.п.) или животных жиров заключается в преобразовании, под действием катализатора, жирных кислот и этанола или метанола (этилового или метилового спирта) в этиловый или метиловый, соответственно, сложный эфир. Побочным неизбежным продуктом этой реакции является глицерин. Разделение этих продуктов может быть осуществлено как в отстойнике, так и в центрифуге. Глицерин – тяжелая фракция, он оседает на дно сосуда. Биодизель – легкая фракция – всплывает наверх. В традиционной технологии разделение происходит медленно, операция может длиться 5-10 часов, также как и сама реакция преобразования жирных кислот и спирта в сложный эфир, если она проводится без механического перемешивания реагентов.
Рис. 2 - Типовая технологическая схема комплексной переработки отходов
Ультразвуковая обработка реагентов позволяет проводить реакцию преобразования в «динамике», т.е. в непрерывном потоке, сокращая время их обработки с 1-4 часов при «пакетной» обработке механическим перемешиванием в несколько, а то и десяток, раз. Еще важнее то, что ультразвуковая обработка снижает также время процесса разделения (биодизеля и глицерина) с 5-10 часов до менее чем 60 минут, который проводится в отстойнике.
При ультразвуковой обработке сырья на 50 % снижается количество используемого катализатора за счет увеличения его химической активности в присутствии кавитации. При использовании ультразвука сокращается количество алкоголя, необходимое для протекания реакции, и, как следствие, увеличивается чистота глицерина.
Ультразвуковая технология производства биодизеля предполагает следующие этапы:
Растительное масло и животные жиры смешивается с этиловым спиртом (этиловым эфиром) или метиловым спиртом (метиловым эфиром) и гидроксидом калия (едкий калий) или натрия (едкий натрий, в просторечии называемый «щелок»).
Смесь подогревается до температуры 45-65 ºС.
Подогретая смесь прокачивается насосом через ультразвуковой реактор.
Глицерин отделяется от биодизеля.
Биодизель омывается водой (в том же ультразвуковом реакторе).
Реакция между компонентами в ультразвуковом реакторе проводится при повышенном давлении, равном 1-5 атмосфер, создаваемом масляным насосом и регулируемым предохранительным клапаном.
В таблице 1 приведены типовые требования к мощности ультразвукового преобразователя реактора при производстве биодизеля в зависимости от производительности установки (количества обрабатываемого сырья, т.е. скорости потока).
Таблица 1
Производительность |
Необходимая мощность |
200-750 л/час |
1 – 2 кВт |
800-3000 л/час |
4 – 6 кВт |
3-12 м3/час |
20 кВт |
20-70 м3/час |
100 кВт |
200-700 м3/час |
1000 кВт |
Практически, энергетические потребности процесса определяются в результате предварительной обработки и существенно зависят от качества исходного сырья.
Для небольших фермерских хозяйств разработана ультразвуковая установка для переработки сырья в биодизель производительностью 50 л/час. Это, так называемая, «лабораторная установка», она используется нашими специалистами для первоначальных исследований и демонстрации процесса. Схема установки показана на рис. 3.
В состав установки входит следующее оборудование:
ультразвуковой генератор мощностью 1 кВт с рабочей частотой 22 кГц;
ультразвуковой преобразователь мощностью 500 Вт или 1 кВт, с концентратором, волноводом и реактором;
рабочая емкость (бак, 80 литров, пластик HDPE);
нагреватель 1-2 кВт;
емкость катализатора (бак, 10 литров, пластик HDPE);
механическая мешалка;
масляный насос, производительностью 10-20 л/мин и создающий давление до 5 атмосфер;
клапан обратного давления для регулирования давления и скорости потока;
манометр для измерения давления подачи;
дополнительные емкости для операции разделения биодизеля и глицерина (пластик HDPE).
Для активации работы катализатора в емкости, для его подготовки, смешивается метанол (около 8,5 литров) и гидроксид калия (0,2-0,4 кг). В рабочую емкость заливается 66 литров растительного масла и подогревается до температуры 45-65 ºС.
Когда катализатор полностью распущен в метаноле, катализатор-премикс смешивается в рабочей емкости с подогретым маслом. Насос прокачивает содержимое емкости под давлением 1-5 атмосфер. Циркуляция (оборот) всего содержимого рабочей емкости должна осуществляться за время, приблизительно, 20 минут. За это время происходит реакция преобразования смеси в биодизельное топливо.
Рис. 3 – Схема установки для получения биодизеля
После этого насос и ультразвук отключаются и начинается процесс разделения биодизеля и глицерина, который длится от 30 до 60 минут. После завершения разделения глицерин нужно удалить. Процесс разделения можно проводить в отдельной емкости для отстаивания, что позволит увеличить производительность установки за счет более рационального использования рабочей емкости только для проведения реакции преобразования.
Если исходное сырье качественное, то биодизельное топливо не требует дополнительной очистки, но, как правило, требуется промывка биодизеля водой для удаления примесей.
Для очистки биодизельное топливо смешивается с водой под действием ультразвука в том же реакторе. При этом нужно строго соблюдать технологический режим, поскольку при нарушении режима возможно образование стабильной эмульсии воды и биодизеля, что потребует для разделения такой смеси применения специального оборудования, например центрифуги.
Технологический процесс производства биодизельного топлива в значительной степени зависит от качества исходного сырья, поэтому в каждом конкретном случае необходимо корректировать технологию под имеющееся сырье.
На рис. 4 показана типовая схема завода для промышленного производства биодизеля. Основой данной системы служит ультразвуковой реактор непрерывной обработки сырья и установка непрерывного разделения биодизеля и глицерина.
Для непрерывной обработки подогретое масло и катализатор смешиваются порционально-постоянно, используя для этого регулируемые насосы. Встроенный смеситель улучшает однородность сырья перед подачей его в ультразвуковой реактор. В реакторе, в условиях ультразвуковой кавитации, реагенты находятся около 30 секунд. Значения давления, температуры и прочих показателей контролируются автоматикой и используются в системе автоматического регулирования процесса производства.
Рис. 4 - Типовая схема завода для промышленного производства биодизеля.
После ультразвуковой обработки смесь закачивается в установку непрерывного разделения, выполненную в виде колонны. Объем емкости установки разделения должен обеспечить удержание (нахождение) смеси в колонне в течение времени, примерно, около 1 часа. В течение этого времени реакция преобразования будет окончательно завершена.
Далее, отреагировавшая смесь биодизеля и глицерина закачиваются в центрифугу, где происходит окончательное разделение на фракции. Дальнейшая обработка предполагает восстановление алкоголя, очистку и осушку, которые тоже выполняются в непрерывном режиме.
Необходимо особо отметить тот факт, что гидроксиды калия и натрия являются сильными щелочами и могут стать причиной ожогов на коже, а метанол – сильнейший яд, он является очень токсичным и взрывоопасным, при применении внутрь – 30 г является смертельной дозой; может впитываться в организм через кожу, вызывая отравление и слепоту. Поэтому, применение этих веществ требует строжайшего соблюдения правил и требований техники безопасности и охраны труда, а также хорошей вентиляции помещений. В связи с этим, более предпочтительным является использование этилового спирта.
Биодизельное топливо, например, рапсовый метиловый эфир (RME) обладает рядом преимуществ по сравнению с прямым растительным маслом (SVO). It requires no engine conversion or fuel system modification to run biodiesel on conventional diesel engines. Оно не требует какой-либо переделки двигателя или топливной системы, его можно спокойно использовать на обычных дизельных двигателях, особенно на современных, поскольку оно практически не содержит серы. Biodiesel is commonly added to the petrodiesel sold at pumps today to increase the lubricity of pure Ultra-Low Sulfur Diesel (ULSD), which is advantageous since Biodiesel has almost no sulfur content.В двигателях старых конструкций длительная работа на 100%-ном биодизельном топливе может вызвать осложнения на увлажненных резиновых изделиях (уплотнения, шланги, сальники). Замена их на современные силиконовые уплотнения решает эти проблемы. Также можно предотвратить эти проблемы, смешивая 90-75 % биодизеля и 10-25 % нефтяного дизтоплива.
Для внедрения этих технологий производства биогаза и биодизеля на Вашем производстве необходимы исходные данные по сырью и объемам продукции для переработки. Проектирование и изготовление ультразвукового оборудования осуществляет Научно-Производственная Лаборатория «Ультра Звуковые Технологии». Разработка технологического процесса выполняется совместно с Институтом биоорганической и нефтехимии (ИБОНХ) АН Украины.
28.02.2009
Зав. Лаборатории Валерий Буряков
Техн. директор Александр Кореневич