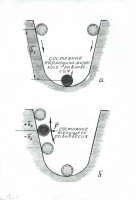
Ультразвук в металлургии
Секреты Гефеста
Во все времена, а в условиях кризиса особенно, думающие о будущем предприниматели и руководители предприятий активно занимались реконструкцией и модернизацией своего производства. Это позволяет выйти из кризиса на более высокой ступени развития предприятия и технологии производства. И этой статье мы попытаемся рассказать о возможностях и перспективах практического применения ультразвуковых методов для повышения качества металла и интенсификации технологических процессов при получении изделий.
Мощный ультразвук является средством активного воздействия на протекание тепломассообменных процессов в жидкости, на структуру и свойства твердых тел и на процессы их контактного взаимодействия, что позволяет интенсифицировать технологические процессы получения и обработки материалов.
Современные ультразвуковые генераторы и преобразователи, изготовленные с использованием современной элементной базы, позволяют внедрять научные разработки в действующие технологические процессы уже сегодня. При этом ультразвуковое оборудование обладает высоким к.п.д. и низким энергопотреблением. Для воздействия на технологические процессы получения и обработки материалов используются ультразвуковые колебания относительно высокой интенсивности (более 1 Вт/см2), вызывающие необратимые изменения в облучаемой среде.
Ультразвук с успехом применяется для дегазации расплавленного металла, улучшения качества слитка и отливки, интенсификации процессов зонной перекристаллизации и выращивания кристаллов, металлизации трудносмачиваемых подложек, распыления расплавов для получения порошков, создания псевдосплавов типа «замороженных» эмульсий и суспензий, удаление керамических стержней, выщелачивание и очистка отливок, ускорения электрохимических процессов, очистки изделий и многих других процессов.
Далее приведем несколько примеров ультразвуковой обработки металлов, которые можно сегодня перенести из стадии лабораторных исследований в стадию промышленного освоения. Для успешной реализации процесса индустриального освоения создано пригодное для промышленного использования ультразвуковое оборудование, разработаны методы и технологии ультразвуковой обработки. Необходимы лишь небольшие исследования и эксперименты в условиях заводских лабораторий для привязки оборудования к конкретным производствам.
Рассматривая механизмы воздействия ультразвука на процессы дегазации и кристаллизации металлов отметим, что воздействие мощных ультразвуковых колебаний на расплав металла приводит к его дегазации. Основную роль в этом процессе играет кавитация и упругие колебания обрабатываемой среды. Непосредственным результатом ультразвуковых колебаний на кристаллизующийся металл являются структурные изменения, происходящие в слитке (отливке). В обработанном ультразвуком металле наблюдается устранение столбчатой структуры, образование мелкого равноосного зерна, повышение однородности слитка и уменьшение степени развития ликвационных процессов.
Структурные изменения, происходящие в слитке, определяются процессами, протекающими в расплаве и двухфазной зоне – зарождением кристаллов, их диспергированием, процессами перемешивания, которые связаны с развитием в расплаве кавитации и акустических потоков. И зависят от условий кристаллизации и свойств обрабатываемого материала.
Свойства обрабатываемого материала определяют параметры ультразвукового поля в расплаве: частота колебаний; величина колебательного давления и скорости; потери в среде и т. п.
Условия дегазации и температура расплава определяют его вязкость и величину поверхностного натяжения в системе жидкость-пар.
Условия кристаллизации металла (скорость роста кристаллов и градиент температур в жидкости у фронта кристаллизации) оказывают существенное влияние на структуру фронта и ширину двухфазной зоны и, тем самым, на параметры ультразвукового поля в области, примыкающей к границе раздела твердой и жидкой фаз.
Ультразвуковая энергия, вводимая в расплав, является причиной возникновения в нем избыточных давлений и перемешивания, изменяющих кинетику процесса кристаллизации.
В исследованиях и работах Г.И.Эскина оценена эффективность ультразвуковой дегазации по сравнению с другими известными методами удаления газа – рафинированием расплава алюминия хлористыми солями и вакуумированием. Вакуумирование оказывает больший эффект на дегазацию, чем флюсы, ультразвук – еще больший. Совместное действие ультразвука и вакуумирования ведет к дополнительному ускорению процесса и снижению предела газонасыщенности сплава. Такая совместная обработка расплава ультразвуком и вакуумирования представляет собой один из наиболее перспективных способов получения плотных высококачественных слитков алюминиевых сплавов.
Проведенные эксперименты показали возможность эффективного ультразвукового рафинирования промышленных стационарных объемов и потока расплава при непрерывном литье больших масс расплава. В результате ультразвуковой обработки расплава повышается чистота слитков, увеличивается жидкотекучесть при оформлении сечений фасонных отливок, повышается плотность литого и деформированного металла, улучшается качество слитка (отливки).
Анализ процессов кристаллизации металлов в ультразвуковом поле показывает, что обрабатываемость материалов определяется эффективностью проникновения ультразвука в объем расплава и к фронту кристаллизации, которая, в свою очередь, зависит от способа введения колебаний в расплав. Способы введения ультразвуковых колебаний связанны с существующими процессами получения отливок и слитков, для которых возможно и целесообразно применение ультразвуковой обработки. К указанным процессам относится получение слитков и отливок в формах и изложницах, и слитков в машинах непрерывного литья или при рафинирующих (вакуумно-дуговом, электрошлаковом и электронно-лучевом) переплавах. Введение ультразвуковых колебаний при непрерывной разливке может производится через струю расплава или через кристаллизатор и/или через корочку слитка в зоне вторичного охлаждения слитка.
Одним из наиболее рациональных способов является обработка металла в процессе непрерывного литья. Постоянное и не очень значительное количество металла, кристаллизующегося в единицу времени, делает возможным использование для его обработки источников ультразвуковых колебаний сравнительно небольшой мощности.
При ультразвуковой обработке металлов и сплавов, наряду с измельчением зерна, под действием ультразвука происходит изменение характера распределение характера распределения фаз и уменьшается степень развития зональной и дендритной ликвации. Все эти эффекты влияют на изменение свойств сплавов независимо от типа кристаллической решетки. Кроме того, значительно повышается предел прочности и повышаются характеристики пластичности металлов. Измельчение структуры слитка при ультразвуковой обработке приводит к переходу от дендритной к субдендритной структуре.
Многие металлы, подвергнутые ультразвуковой обработке, обладают повышенной коррозионной стойкостью и ударной вязкостью. Наиболее эффективной является ультразвуковая обработка цветных металлов, сталей ферритного, аустенитного и карбидного классов, углеродистых и низколегированных сталей, сталей с высоким содержанием бора, чугунов и т. п.
Весьма эффективным является также применение ультразвука в процессах зонной перекристаллизации (очистки) металлов. Анализ явлений, наблюдаемых при введении ультразвука в жидкие среды, показывает, что ультразвук, не только вызывает интенсивное перемешивание жидкости, но и оказывает воздействие на диффузионные процессы. Существует несколько способов введения ультразвука в процессе зонной очистки. При определенных параметрах ультразвука значительно интенсифицируется процесс очистки, повышается чистота металла, примесь концентрируется только в конце слитка. Положительные результаты получены при обработке черных, цветных, полупроводниковых, редкоземельных металлов и сплавов.
К работам по зонной и направленной кристаллизации под воздействием ультразвука непосредственно примыкают эксперименты по использованию ультразвука в процессе вакуумной дистилляционной очистки. Использование ультразвука при очистке олова от летучих примесей вакуумной дистилляцией позволило в среднем на порядок повысить степень очистки по сравнению с обычным прогревом.
Ультразвук не только позволяет улучшить структуру и свойства металлов и сплавов, но и может быть использован для получения методами литья композитных сплавов из не сплавляемых в обычных условиях материалов (металла и окислов, боридов и др.). Применение ультразвука позволяет получать методами литья композитные сплавы из компонентов, не растворимых в жидком состоянии – «замороженных» металлические эмульсии и суспензии.
При получении сплавов типа «замороженных» эмульсий из компонентов, имеющих область расслаивания в жидком состоянии, процесс введения второго компонента осуществляется при температуре, превышающей температуру расслоения. После достижения состояния однородного распределения второго компонента (образования раствора) расплав закристаллизовывается в условиях, препятствующих расслоению.
При получении сплавов типа «замороженных» суспензий в расплавленный металл-основу вводят порошок-наполнитель и подвергают расплав ультразвуковой обработке. Режим обработки зависит от природы металла-основы и порошка-наполнителя, их концентрации и дисперсности. Основную роль в этих процессах играет кавитация, возникающая под действием ультразвука.
Многие отрасли промышленности используют изделия, полученные методами порошковой металлургии. Одним из возможных путей реализации процесса распыления жидкого металла может является применение ультразвуковых колебаний, под действием которых, на границе раздела жидкость-газ или на свободной поверхности жидкости происходит процесс каплеобразования. Анализ процесса показывает, что акустическая энергия может быть подведена к зоне распыления, как со стороны жидкости, так и со стороны газа при диспергировании (распылении) сплавов. В соответствии с этим, способы распыления можно классифицировать как ультразвуковое жидкостное и ультразвуковое пневматическое распыление.
Использование ультразвукового метода распыления позволяет получить порошки металлов более однородное по фракционному составу, при этом повышается выход годного продукта, гранулометрический состав порошка становится более мелким, а расход газа-распылителя может быть уменьшен, содержание кислорода в материале на порядок меньше чем после общепринятого пневматического распыления. Испытания режущих свойств резцов, изготовленных из материала 10Р6М5, полученного пневматическим и пневмоакустическим распылением, показали, что износостойкость «ультразвуковых» изделий в 1,2–1,5 раза выше износостойкости изделий, изготовленных по принятой технологии.
Более детально с вышеописанными процессами можно познакомиться в работах д.т.н. профессора О.В.Абрамова, Г.И.Погодина-Алексеева, Г.И.Эскина и многих других ученых, внесших огромный вклад в развитие ультразвуковых технологий обработки материалов.
Введение ультразвука высокой интенсивности в металл, в твердом состоянии, вызывает увеличение плотности структурных несовершенств (дислокаций, вакансий), что приводит к изменению свойств подвергаемого обработке материала и оказывает влияние на процесс пластической деформации.
На границе раздела твердая фаза-твердая фаза ультразвуковые колебания приводят к изменению состояния поверхностного слоя, вследствии чего уменьшаются силы граничного трения при перемещении одного тела по другому. Эти процессы открывают возможность использования ультразвука в процессах обработки металлов давлением, дает возможность снизить энергетические затраты, увеличить скорость процесса деформирования, повысить стойкость инструмента, улучшить качество поверхности изделий, осуществить процесс деформации таких материалов, которые разрушаются при обычных способах обработки давлением.
Работы по исследованию влияния ультразвуковых колебаний на механические свойства металлов проводились Б.Лангенекером в 50-х годах ХХ века, далее академиком В.П.Северденко и его учениками В.В.Клубовичем и А.В.Степаненко. К настоящему времени абсолютно доказана эффективность применения ультразвука в процессах волочения проволоки и труб, прессования, ковки, штамповки и прокатки, волочения «микронной» проволоки и т.п. Ультразвуковая волока радиальных колебаний позволяет сегодня работать на скоростях до 1000 м/мин при волочении проволоки, что дает возможность увеличить скорость, улучшить качество и значительно снизить энергозатраты в процессе волочения труб, увеличить стойкость волоки и т.д. и т.п.
Исследования показали, что ультразвуковое воздействие на металл, в процессе его термической или химико-термической обработки, является одним из наиболее эффективных методов обработки. При ультразвуковой обработке получены результаты, не достижимые при обычной термообработке, и позволяющие значительно сократить длительность технологического цикла обработки. Наложение ультразвукового поля активно влияет на диффузионные процессы, на процессы фазовой перекристаллизации, старение и отпуск, закалку, химико-термическую обработку металлов.
Одним из наиболее распространенных направлений использования ультразвука является очистка поверхностей от окалины, жировых, механических и химических загрязнений. Основными преимуществами ультразвуковой очистки можно считать ее высокое качество, технологичность, относительную простоту оборудования. Ультразвуковые преобразователи способны работать в растворах щелочей, кислот, смеси кислот и любых моющих средствах как в низко- так и высокотемпературных режимах. Использование ультразвука позволяет механизировать процессы очистки, обеспечивая высокое качество продукции и стабильность процесса.
Внедрение ультразвукового технологического оборудования позволяет экономить огромные средства, особенно если ультразвуковые установки для обработки могут быть включены в автоматическую или полуавтоматическую действующую линию или технологический процесс, а это возможно во многих случаях благодаря встраиваемым ультразвуковым блокам.
Ультразвуковая очистка наиболее эффективна при обработке сложных поверхностей в машиностроении и может с успехом применяться для обработки листов, лент, труб, проката, проволоки и т.п. в крупносерийном и массовом производстве. Высокоамплитудная ультразвуковая очистка в комбинации с электрохимическими методами дает возможность очищать изделия в динамике, на высоких скоростях. Например, на стане волочения проволоки на скорости до 500 м/мин и выше. Решающим фактором в производственных процессах очистки является кавитация.
Специалистам хорошо известны проблемы удаления керамических стержней из полых отливок. Эта тяжелая и вредная ручная работа отбойным пневматическим молотком, а затем дробеструйная обработка может быть успешно заменена ультразвуковой выбивкой и/или выщелачиванием керамических стержней. Ультразвук позволяет механизировать процесс, ускорить его до 30–180 сек. Такая технология значительно снижает трудоемкость, устраняет вредное влияние вибраций и шума от пневмоинструмента, значительно улучшаются условия труда, повышая эффективность использования оборудования, приносит значительный экономический эффект.
При прохождении ультразвука через границу металл заготовки-керамика стержня, из-за разницы в скоростях распространения звуковых волн в этих средах, в их пограничных зонах возникают механические напряжения, разрушающие более хрупкую среду – керамический стержень. Эвакуация разрушенной керамики из полости заготовки происходит благодаря вибрациям отливки в результате воздействия на нее ультразвукового инструмента. Приведем один пример: при удалении керамических стержней из отливок лопаток турбины, длинной 520 мм из жаропрочных сплавов, при массе заготовки 12 кг и массе стержня 0,25_кг – машинное время операции составляет 2 мин, а качество очистки несоизмеримо с традиционными методами.
Далее рассмотрим интенсификацию электрохимических процессов в ультразвуковом поле. Использование ультразвуковых колебаний для интенсификации электрохимических процессов не требует существенного переоборудования имеющихся на производстве гальванических ванн. При воздействии ультразвука на процессы электролитического осаждения металла значительно увеличиваются предельно допустимые плотности тока, возрастает скорость осаждения металла, снижается перенапряжение на электродах, устраняется явление пассивирования поверхности анодов в процессе электроосаждения, осаждаемый металл имеет явно выраженную мелкокристаллическую структуру, уменьшается пористость и шероховатость поверхности, улучшается адгезия (сцепление) покрытия с основным металлом. В некоторых электролитах можно получать блестящие осадки без добавления блескообразователя. Ультразвук применяют при меднении и электролитическом рафинировании меди, никелировании, хромировании, кадмировании, латунировании, цинковании, серебрении, золочении и т.п. Применение ультразвука в десятки раз повышает значение предельно допустимой плотности тока, в 10–15 раз увеличивает скорость осаждения металла с одновременным улучшением качества покрытия.
Мы вкратце описали лишь некоторые, основные точки приложения ультразвука в Ваших технологиях. Использование ультразвуковых технологий в Вашем производстве позволит Вам повысить конкурентноспособность и улучшить качество продукции, получить значительный экономический эффект, внедрить на своем предприятии передовые, экологически чистые, энергосберегающие технологии.
Ультразвуковые преобразователи легко встраиваются в уже работающее технологическое оборудование, что дает возможность модернизации существующего производства. Современное ультразвуковое оборудование, разработанное и изготовленное Научно-Производственной Лабораторией «Ультра Звуковые Технологии», способно работать круглосуточно, в автоматическом режиме и не требует специально обученного персонала. Все детали, контактирующие с агрессивными средами, выполнены из титана или пищевых нержавеющих сталей. И самое главное: ультразвук – это абсолютно безвредный, экологически чистый «инструмент» эффективной интенсификации различных процессов. Инструмент, способный улучшить качество продукции и принести значительные экономические выгоды Вашему предприятию.
15.11.2008
Зав. Лаборатории Валерий Буряков
Техн. директор Александр Кореневич